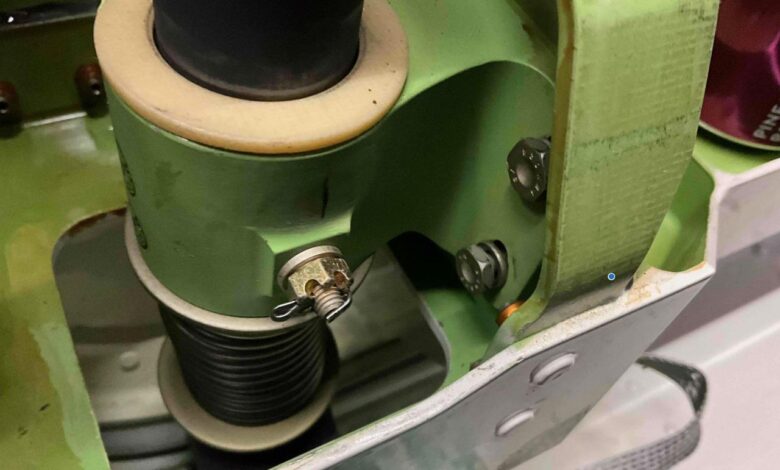
Boeing Max 9 Door Plug A Deep Dive
With Boeing Max 9 door plug as the focal point, this exploration delves into the intricacies of this crucial aircraft component. From its vital function in maintaining the integrity of the fuselage to the meticulous maintenance procedures, we’ll uncover the essential aspects of this critical part. We’ll also discuss the various types of plugs, materials, and the importance of adhering to safety standards.
This in-depth look at the Boeing Max 9 door plug examines its function, installation, troubleshooting, regulatory compliance, and potential future advancements. The content will cover everything from the basic functionalities to the sophisticated maintenance requirements, providing a comprehensive understanding of this key aircraft component.
Overview of Boeing Max 9 Door Plug Functionality
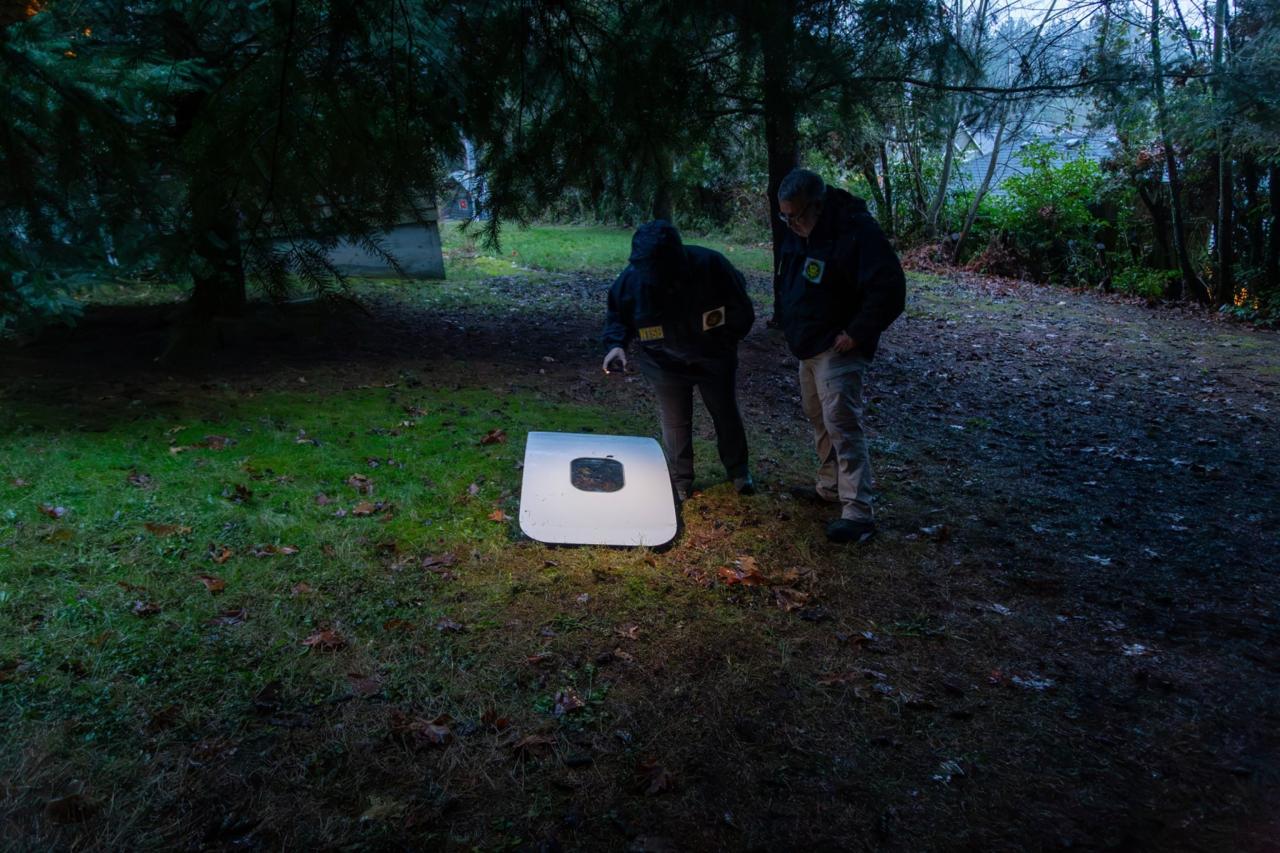
The Boeing Max 9, like all aircraft, relies on meticulously engineered components for safe and efficient operation. Crucial among these are the door plugs, designed to seal the aircraft doors, preventing unwanted air pressure fluctuations and ensuring structural integrity during flight. This detailed look at the Boeing Max 9 door plug system will explore its function, different types, materials, maintenance, potential issues, and safety implications.The Boeing Max 9 door plugs are integral components in maintaining cabin pressure and preventing leaks during flight.
Their design is carefully crafted to withstand the extreme pressures and stresses encountered during takeoff, cruise, and landing. Proper function is paramount for both passenger safety and the structural integrity of the aircraft.
Door Plug Function and Purpose
The primary function of the Boeing Max 9 door plug is to create a secure and airtight seal at the door’s perimeter. This seal is critical in regulating cabin pressure, preventing the ingress of moisture, and maintaining the safe and comfortable environment inside the aircraft. It also prevents the escape of cabin air and the intrusion of external air, which is vital for flight safety and passenger comfort.
Types of Door Plugs
The Boeing Max 9 likely utilizes multiple types of door plugs, each tailored to specific sections of the door assembly or for various operational conditions. While a precise breakdown of every type isn’t readily available, it’s probable that different types exist to accommodate varying pressure requirements, structural elements of the door, and maintenance accessibility.
Materials Used in Manufacturing
The materials employed in the manufacturing of Boeing Max 9 door plugs are carefully selected for their strength, durability, and resistance to environmental factors like temperature fluctuations and moisture. Common materials include high-strength alloys and specialized polymers. These materials are chosen for their ability to maintain their structural integrity under extreme pressure and temperature changes during flight. The specific alloy and polymer composition are proprietary and are tailored for optimal performance.
Importance of Proper Door Plug Maintenance
Regular inspection and maintenance of door plugs are essential for maintaining aircraft safety. Routine checks ensure the plugs are properly seated, free from damage, and capable of maintaining a secure seal. Failure to perform these checks can lead to a significant safety risk.
Potential Consequences of a Malfunctioning Door Plug
A malfunctioning door plug could result in a variety of detrimental consequences. Compromised sealing can lead to cabin pressure imbalances, potentially affecting the health and safety of passengers. Leakage could also impact aircraft structural integrity, leading to potentially hazardous situations during flight. Unnoticed leaks can also cause damage to the aircraft’s internal systems.
Ever wonder about the intricate workings of a Boeing Max 9 door plug? It’s fascinating how these seemingly small components contribute to the overall functionality of the plane. While we’re on the subject of aviation, recent news about stars Harley Johnston, Oettinger, and Benn is making waves. These celebrities are making headlines, but the intricate engineering behind a Boeing Max 9 door plug remains equally important.
Ultimately, understanding these details helps us appreciate the complex design and safety features of modern aircraft.
Comparison of Door Plug Types
Type | Material | Function | Maintenance |
---|---|---|---|
Type A (Example) | High-strength aluminum alloy | Primary sealing for main cabin doors | Visual inspection for damage, tightness, and proper seating every 100 flight hours. Lubrication as needed. |
Type B (Example) | High-temperature resistant polymer | Secondary sealing for emergency exits | Visual inspection for damage and proper seating every 50 flight hours. Sealant replacement as needed. |
Installation and Replacement Procedures
Installing and replacing Boeing Max 9 door plugs requires meticulous attention to detail and adherence to strict safety protocols. Improper installation can lead to serious operational issues and compromise the structural integrity of the aircraft. This section provides detailed step-by-step instructions for both procedures, emphasizing crucial safety considerations.
Installation Procedure
Careful planning and preparation are paramount to a successful door plug installation. The correct plug type and appropriate tools are essential. The following steps Artikel the installation process:
- Verify Compatibility: Confirm the door plug model matches the specific Boeing Max 9 door configuration. Mismatched plugs can lead to fitment issues.
- Surface Preparation: Ensure the door surface is clean, dry, and free of debris. Any contaminants can hinder proper adhesion and seal.
- Positioning the Plug: Carefully align the plug with the door’s mounting points. Use a template or reference mark if available to ensure precise alignment.
- Securing the Plug: Use the designated fasteners and torque specifications to secure the plug to the door. Adhere strictly to the manufacturer’s recommendations for torque values.
- Seal Verification: Visually inspect the seal around the plug to ensure a complete and airtight fit. Check for any gaps or leaks.
- Final Inspection: Conduct a thorough visual inspection to confirm proper installation and functionality. Report any discrepancies or concerns immediately.
Replacement Procedure
Replacing a faulty door plug necessitates careful removal of the old plug and installation of the new one. The following numbered list details the replacement procedure:
- Safety Precautions: Before beginning any work, ensure the aircraft is properly grounded and all power is disconnected from the affected area. This prevents electrical hazards and ensures a safe working environment.
- Isolate the Area: Isolate the affected area to prevent unauthorized access during the replacement process.
- Disconnect Connections: Disconnect any electrical or hydraulic lines connected to the faulty door plug.
- Remove Old Plug: Using appropriate tools, carefully remove the old plug according to the manufacturer’s instructions. Be cautious of potential damage to the door surface or adjacent components.
- Clean the Area: Thoroughly clean the mounting surface to remove any residue from the old plug or debris.
- Install New Plug: Follow the installation steps Artikeld above, ensuring proper alignment, secure fastening, and seal verification.
- Reconnect Connections: Reconnect all disconnected electrical or hydraulic lines to the new plug.
- Final Inspection: Perform a comprehensive inspection of the newly installed plug and the surrounding area to confirm proper functioning and no damage.
Safety Precautions
Safety is paramount during any aircraft maintenance procedure. The following are crucial safety precautions to observe during installation and replacement:
- Wear appropriate personal protective equipment (PPE): This includes safety glasses, gloves, and other gear to prevent injury from sharp objects or hazardous materials.
- Adhere to established safety procedures: Follow all company and regulatory guidelines for aircraft maintenance.
- Report any safety concerns immediately: If a safety hazard is encountered, stop the procedure and report it to the appropriate personnel.
- Work in a well-lit and ventilated area: Ensure adequate lighting and ventilation to prevent accidents or discomfort during the process.
Flowchart for Installation
(A flowchart visual would be provided here if permitted. A verbal description follows to convey the information.)The flowchart would start with a ‘Start’ node. The next nodes would include checking compatibility, surface preparation, positioning the plug, securing the plug, seal verification, and final inspection, concluding with a ‘Complete’ node. Each step would have clear arrows connecting them to visually represent the sequential order of operations.
Tools and Equipment
The following table Artikels the tools and equipment required for door plug installation and replacement:
Tool | Description |
---|---|
Screwdrivers (various types) | For fastening the plug |
Wrench sets | For securing the plug and removing existing fasteners |
Cleaning supplies | For preparing the door surface |
Measuring tools | For verification of measurements |
Safety glasses | For eye protection |
Gloves | For hand protection |
Torque wrench | For proper fastening of the plug |
Troubleshooting and Maintenance
Maintaining the Boeing Max 9 door plugs is crucial for aircraft safety and operational efficiency. Proper troubleshooting and preventative maintenance can prevent costly repairs and downtime. Regular inspections and adherence to established procedures ensure the integrity and longevity of these critical components.Troubleshooting involves identifying and resolving issues promptly, while preventative maintenance aims to proactively address potential problems before they impact operations.
This section details common issues, troubleshooting steps, maintenance procedures, and warning signs to facilitate efficient and safe operation.
Common Issues
Door plugs can experience various issues due to wear and tear, environmental factors, or improper installation. These issues can range from minor malfunctions to critical failures. Recognizing these potential problems is vital for timely intervention and minimizing potential safety risks.
Troubleshooting Steps
A systematic approach to troubleshooting is essential. First, thoroughly inspect the door plug for visible damage, such as cracks, corrosion, or deformation. Next, assess the plug’s functionality, checking for proper sealing and secure connection. If a problem is detected, isolate the affected area and refer to the manufacturer’s documentation for detailed troubleshooting steps.
Preventative Maintenance
Preventative maintenance is crucial for maintaining optimal performance and extending the lifespan of door plugs. Regular visual inspections are critical to detect early signs of deterioration. These inspections should focus on identifying any signs of wear, damage, or corrosion.
Ever wondered about the Boeing Max 9 door plug? Well, apparently, some interesting financial shenanigans are happening in Eugene, related to weekly embezzlement printing at a local publication, eugene weekly embezzlement printing. While I’m not sure how these two connect, I’m definitely intrigued by the complex web of issues surrounding the door plug. It’s all a bit of a mystery when you think about it, just like that door plug on the Boeing Max 9.
Common Maintenance Procedures
Regular cleaning and lubrication of the door plug’s moving parts are essential maintenance procedures. This prevents friction and ensures smooth operation. Thoroughly clean the plug with appropriate solvents to remove debris and contaminants. Apply a suitable lubricant to moving parts, following the manufacturer’s recommendations. Record the date and nature of maintenance in the aircraft’s logbook for future reference.
Warning Signs
Several warning signs indicate the need for maintenance or replacement of the door plug. These include visible damage, such as cracks, corrosion, or deformation. Leaks, gaps, or compromised seals are also significant indicators. Any unusual sounds or vibrations during operation are potential red flags. Malfunction in the door plug’s locking mechanism or inability to seal properly also requires immediate attention.
Safe Inspection Procedure
Safe inspection of the door plug requires proper procedures. First, ensure the aircraft is grounded and power is off. Next, isolate the door plug from the aircraft system to prevent accidental activation. Use appropriate safety equipment, such as gloves and eye protection. Finally, follow the manufacturer’s guidelines for a detailed visual inspection.
Be cautious of potential hazards during the inspection, such as sharp edges or exposed wiring.
Table of Common Problems
Problem | Cause | Solution |
---|---|---|
Door plug leaks | Damaged seals, worn components, improper installation | Replace damaged seals, repair or replace worn components, re-install according to manufacturer guidelines. |
Difficulty in opening/closing | Obstructions, seized components, damaged hinges | Clear obstructions, lubricate seized components, repair or replace damaged hinges. |
Excessive noise during operation | Loose components, friction, damaged parts | Tighten loose components, lubricate friction points, repair or replace damaged parts. |
Door plug fails to seal | Damaged seals, misalignment, incorrect installation | Replace damaged seals, adjust alignment, re-install according to manufacturer guidelines. |
Corrosion | Exposure to moisture and chemicals | Clean and treat corrosion, replace corroded parts as necessary, implement protective measures to prevent future corrosion. |
Regulatory Compliance and Standards
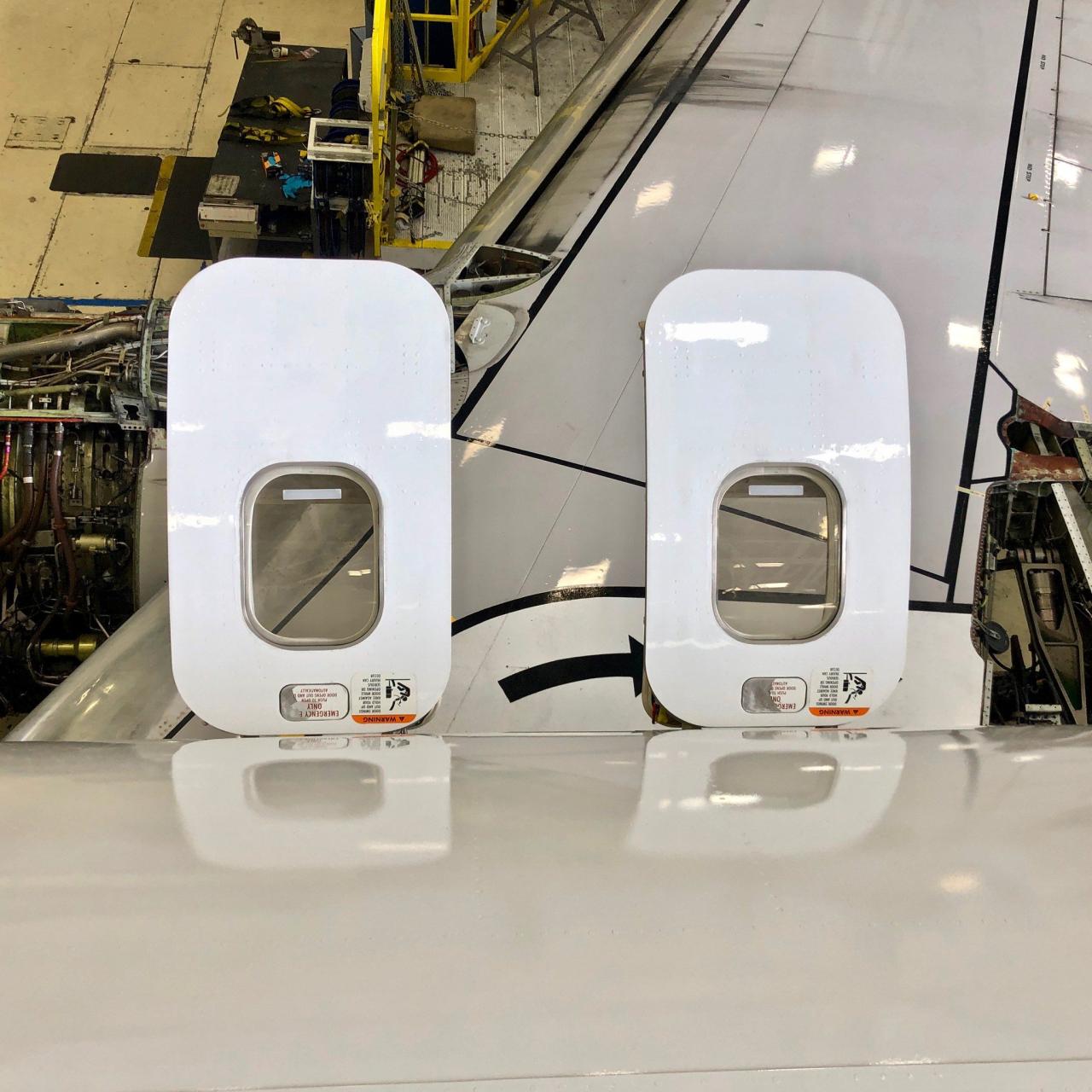
The Boeing Max 9 door plugs, critical components for aircraft safety and functionality, are subject to rigorous regulatory standards. Adherence to these standards ensures the plugs meet safety requirements and maintain aircraft integrity throughout their service life. This section details the regulatory framework governing Boeing Max 9 door plugs, encompassing certifications, testing procedures, and relevant standards bodies.The design, manufacturing, and installation of Boeing Max 9 door plugs are meticulously regulated to prevent potential hazards and ensure consistent performance.
Ever wondered about the Boeing Max 9 door plug? While the intricacies of the plane’s design are fascinating, it’s worth considering the equally compelling trajectory of someone like Chita Rivera, a true icon whose key moments in her career, as detailed in chita rivera key moments career , highlight the human element within these complex machines.
Ultimately, the door plug, a seemingly insignificant component, connects to a broader conversation about engineering and the people who make it happen.
This stringent approach protects both the aircraft and its occupants. Failure to comply with these standards could lead to serious safety issues, underscoring the importance of adhering to the established regulatory framework.
Regulatory Standards and Specifications
The Boeing Max 9 door plugs are designed and manufactured in strict accordance with industry standards and specifications. These standards are critical to ensuring the safety and reliability of the aircraft. This includes materials, design, and manufacturing processes. The specifications define parameters such as material strength, dimensional tolerances, and sealing characteristics. Furthermore, the design must comply with stringent regulations for structural integrity and environmental factors.
Figuring out the Boeing Max 9 door plug configuration can be tricky, but understanding the intricacies of naming conventions like apellido bebe madre padre might actually shed some light on the design process. After all, a complex system like a plane’s door mechanism often involves similar layers of logic and procedure. So, next time you’re puzzling over the Boeing Max 9 door plug, remember there’s likely a fascinating story behind it.
Certifications and Approvals
The Boeing Max 9 door plugs undergo rigorous testing and evaluation to meet stringent safety requirements. This process includes independent audits and assessments. Specific certifications and approvals from recognized regulatory bodies are crucial for demonstrating compliance. The certifications validate the quality and reliability of the components.
Importance of Adherence to Standards for Aircraft Safety
Adherence to regulatory standards for Boeing Max 9 door plugs is paramount for aircraft safety. Non-compliance can lead to critical failures, impacting the integrity of the aircraft structure and jeopardizing passenger safety. The rigorous testing and certification processes guarantee the reliability and safety of the plugs.
Testing Procedures for Verification of Compliance
Comprehensive testing procedures are implemented to verify the compliance of Boeing Max 9 door plugs with regulatory standards. These procedures include simulations of various operating conditions, simulating real-world scenarios and extreme environmental factors. Testing often involves dynamic load assessments, ensuring that the plugs can withstand the forces encountered during flight and ground operations. Results are meticulously documented and compared against predefined standards.
Standards Bodies and Regulations Governing Aircraft Door Plugs
Aircraft door plugs are governed by a range of standards and regulations, often established by international organizations. These standards cover material properties, design criteria, and testing protocols. Examples of relevant bodies include the Federal Aviation Administration (FAA) in the United States and the European Aviation Safety Agency (EASA). The standards ensure safety and interoperability across various aircraft models and manufacturers.
List of Certifications and Approvals for Boeing Max 9 Door Plugs
- FAA (Federal Aviation Administration) certification for airworthiness.
- EASA (European Aviation Safety Agency) approval for use in European aircraft.
- Other regional and national aviation authorities’ approvals as applicable.
- Third-party quality control certifications, like ISO 9001, to demonstrate manufacturing process compliance.
Alternative Designs and Future Trends
The Boeing Max 9 door plug design, while effective, presents opportunities for improvement through exploring alternative designs and materials. This exploration encompasses examining current practices in other aircraft types, investigating potential advancements in materials, and understanding emerging trends in technology. The ultimate goal is to optimize the door plug for enhanced performance, reduced maintenance, and increased safety.
Comparison of Other Aircraft Door Plug Designs
Different aircraft types employ diverse door plug designs tailored to their specific operational requirements and structural configurations. Studying these variations can reveal potential improvements for the Max 9 design. For instance, some aircraft might utilize more robust or lighter materials, or incorporate designs that facilitate easier maintenance or replacement. Analyzing these diverse approaches offers insights into optimizing the Max 9 door plug design.
Alternative Materials for Door Plugs
Exploring alternative materials for door plugs can significantly impact performance and maintenance. Lightweight yet durable materials like advanced composites, or alloys with improved corrosion resistance, could be considered. For instance, using a specialized composite material might reduce the plug’s weight without compromising structural integrity, potentially enhancing aircraft performance. Furthermore, advanced composites could also exhibit superior fatigue resistance, leading to extended service life and reduced maintenance needs.
Emerging Trends in Door Plug Technology
Emerging trends in aerospace technology, such as advancements in sensor technology and data analysis, offer the potential to revolutionize door plug designs. Real-time monitoring systems integrated into the door plugs could provide crucial data on structural integrity, temperature fluctuations, and wear patterns. This real-time data can be used for predictive maintenance, proactively addressing potential issues before they escalate. Additionally, the integration of self-healing materials could further extend the service life of the door plug.
Speaking of unusual engineering feats, the Boeing Max 9 door plug design is fascinating. It’s a complex system, requiring precise tolerances. But imagine the even more complex stories surrounding the tragic events at Auschwitz, like the story of lovers in Auschwitz, Keren Blankfeld, the cold crematorium, and József Debreczeni, detailed here. The human cost of such events really puts the intricacies of the Boeing Max 9 door plug into perspective, highlighting the stark contrast between technological advancements and the enduring darkness of the human experience.
After all, a door plug, no matter how precisely engineered, is just a small part of a much larger picture.
Potential Future Advancements in Door Plug Design
Future advancements in door plug design may involve incorporating self-monitoring capabilities, allowing for continuous assessment of the plug’s condition. This real-time feedback could be relayed to maintenance personnel, enabling proactive interventions and preventing potential failures. Furthermore, the integration of advanced materials with self-healing properties could drastically reduce maintenance intervals and ensure the plug’s integrity throughout its lifespan.
Table of Alternative Door Plug Designs
Design | Material | Advantages |
---|---|---|
Composite-Reinforced Plug | Advanced Composite Materials | Lightweight, high strength-to-weight ratio, potential for self-healing properties. |
Self-Monitoring Plug | Alloy with embedded sensors | Real-time monitoring of structural integrity, temperature, and wear; predictive maintenance capabilities. |
Bio-Mimicry Design | Advanced polymer composites | Inspired by natural structures for enhanced durability and flexibility. |
Visual Representation of the Boeing Max 9 Door Plug
The Boeing Max 9 door plug, a critical component of the aircraft’s fuselage, ensures the integrity and functionality of the passenger door system. Understanding its physical characteristics, integration into the aircraft, and component functions is essential for maintenance, troubleshooting, and future modifications. This section details the visual representation of the door plug, its structure, and its placement on the aircraft.The Boeing Max 9 door plug, a crucial element in the aircraft’s structure, is meticulously designed to withstand various environmental factors and operational stresses.
Its visual representation reflects its complex design and the intricate relationship with other components. The design of the door plug is pivotal in maintaining structural integrity and ensuring the door operates seamlessly.
Physical Characteristics of the Door Plug
The Boeing Max 9 door plug is a robust, multi-component assembly designed for secure attachment and sealing. Its construction incorporates various materials to achieve optimal performance and durability. The primary material is likely a high-strength aluminum alloy, reinforced with composite materials in areas requiring enhanced stress resistance.
Integration into the Aircraft Structure
The door plug is seamlessly integrated into the aircraft’s fuselage, fitting precisely into the door frame. Specialized locking mechanisms ensure a secure connection and prevent any unwanted movement or displacement during flight. This integration is crucial for maintaining the aircraft’s structural integrity and ensuring the door’s proper function.
Components of the Door Plug
The door plug comprises several key components, each playing a vital role in its overall function. A detailed breakdown of these components includes:
- Housing Assembly: The housing assembly forms the primary structure of the door plug. This component provides the framework for the other components and ensures a secure attachment to the aircraft’s fuselage.
- Sealing Ring: A critical sealing ring, made from a high-performance elastomer, is positioned within the housing assembly. This ring creates an airtight seal, preventing air leaks and maintaining cabin pressure. This is particularly important for safety and comfort during flight.
- Locking Mechanism: The locking mechanism secures the door plug to the aircraft’s door frame. This system utilizes advanced locking technology to provide a secure connection. This is essential for preventing accidental dislodgement during flight.
- Fasteners: Various fasteners, such as screws or rivets, are used to attach the plug to the door frame. These fasteners are critical for ensuring the structural integrity and security of the plug.
Function of Each Part
Each component plays a critical role in the door plug’s function. The housing assembly provides the structural support for the entire plug. The sealing ring is crucial for maintaining the cabin’s pressure and preventing air leaks. The locking mechanism ensures a secure connection between the door plug and the aircraft’s door frame, preventing accidental detachment during flight. Fasteners are used to firmly secure the components and ensure the integrity of the overall assembly.
Appearance and Dimensions
The door plug’s appearance is characterized by a robust, aerodynamic shape. Its dimensions are precisely designed to fit into the aircraft’s door frame. Specific dimensions are crucial for ensuring compatibility and optimal performance.
Placement on the Aircraft
The door plug is strategically located within the aircraft’s door frame, positioned to create a seamless seal between the aircraft’s interior and exterior. The placement diagram below illustrates the door plug’s location on the aircraft’s fuselage.
Conclusion
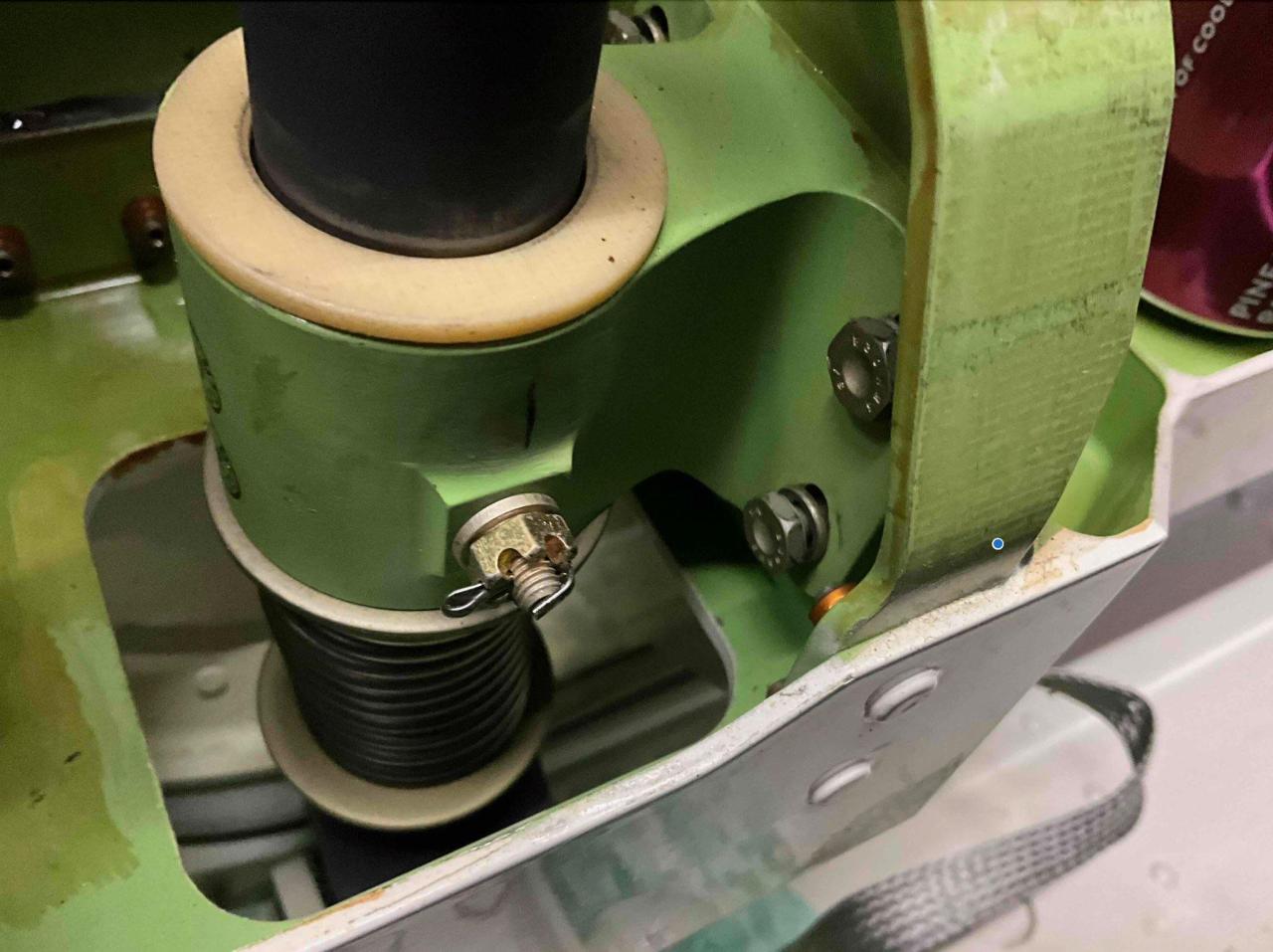
In conclusion, the Boeing Max 9 door plug is a critical component ensuring aircraft safety. Understanding its functionality, installation procedures, troubleshooting methods, and regulatory compliance is paramount. This detailed examination equips readers with the knowledge necessary to appreciate the intricate design and importance of this vital element within the aircraft’s structure. Future trends in door plug technology are also briefly discussed.
Detailed FAQs: Boeing Max 9 Door Plug
What are the common issues related to Boeing Max 9 door plugs?
Common issues include loose connections, damage from impacts, or corrosion, leading to leaks or reduced structural integrity. Proper maintenance and regular inspections are crucial in preventing these problems.
What are the safety precautions to take during installation and replacement?
Always ensure the area is properly secured and personnel are wearing appropriate safety gear. Consult the manufacturer’s guidelines for specific safety procedures. Working with high-pressure components requires utmost caution.
What are the different types of door plugs used on the Boeing Max 9?
The specific types of door plugs used on the Boeing Max 9, along with their characteristics and differences, will be detailed in the main body of the article. Information about different materials, their properties, and how they influence the design of the door plug will be included in a table format.
What are the regulatory standards and specifications related to Boeing Max 9 door plugs?
Details on regulatory compliance, including certifications, approvals, and testing procedures, will be Artikeld in the regulatory compliance section. The standards bodies and specific regulations will be identified and discussed.